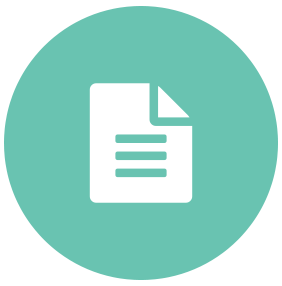
NRDC’s 10 Best Practices for Textile Mills to Save Money and Reduce Pollution - A Practical Guide for Responsible Sourcing Version 2.0
To address the rapidly increasing global effect of this industry, in 2009 NRDC approached a group of multinational apparel retailers and brands to create the Responsible Sourcing Initiative (RSI), a “green supply chain” effort to curb pollution and resource use in the sector while saving the industry money. The Responsible Sourcing Initiative is part of the larger Clean by Design effort NRDC has undertaken to reduce the environmental impacts of the fashion and apparel industries. Clean by Design addresses all major impacts—from fiber growth to dye selection, fabric sourcing to consumer care.
Starting in China, the world’s largest center of manufacturing, NRDC assessed more than a dozen textile mills and conducted in-depth studies of five to identify 10 simple, cost-saving opportunities to reduce water, energy (fuel and electricity), and chemical use via improvements in manufacturing efficiency. In 2011 and 2012, we visited 17 more mills representing a large range of sizes and conditions to apply the 10 Best Practices identified for the mills in the original study and to assess the results. Appendix A provides details on how these assessments were undertaken. We found that all participating mills could benefit substantially from application of the 10 Best Practices, whether large or small, new or old, producing woven or knit goods. Nearly all the facilities—19 out of 22—could benefit from better insulation of their steam pipes, for example, and nearly as many could benefit from better-maintained steam
traps. Insulation of dye tanks provided a valuable opportunity for nearly three-quarters of the mills. Half or more of the facilities could benefit from repairing air leaks in their compressed air systems, which would allow them to reduce the target pressure level and save electricity costs. And half of the mills also had opportunities to recover heat from their air compressor systems or to reuse their condensate.
Starting in China, the world’s largest center of manufacturing, NRDC assessed more than a dozen textile mills and conducted in-depth studies of five to identify 10 simple, cost-saving opportunities to reduce water, energy (fuel and electricity), and chemical use via improvements in manufacturing efficiency. In 2011 and 2012, we visited 17 more mills representing a large range of sizes and conditions to apply the 10 Best Practices identified for the mills in the original study and to assess the results. Appendix A provides details on how these assessments were undertaken. We found that all participating mills could benefit substantially from application of the 10 Best Practices, whether large or small, new or old, producing woven or knit goods. Nearly all the facilities—19 out of 22—could benefit from better insulation of their steam pipes, for example, and nearly as many could benefit from better-maintained steam
traps. Insulation of dye tanks provided a valuable opportunity for nearly three-quarters of the mills. Half or more of the facilities could benefit from repairing air leaks in their compressed air systems, which would allow them to reduce the target pressure level and save electricity costs. And half of the mills also had opportunities to recover heat from their air compressor systems or to reuse their condensate.